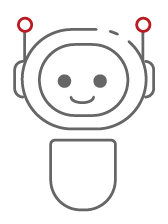
New Productivity, New Production Models, New Resilience
By 2030, digital transformation will have brought a new wave of modernization to enterprises. They will use more productive machines, such as collaborative robots and autonomous mobile robots. New business models will be more people-centric, with increased flexibility in manufacturing, logistics, and other activities. Digitalization will help companies interweave and graphically monitor their supply chains for better resilience in the face of dynamic market environments.
Predictions
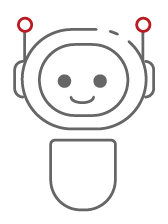
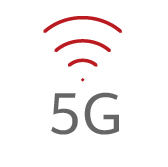

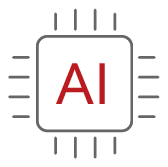
Directions for Exploration

Bringing unmanned operations to manufacturing and services to make up for labor shortages
Snapshot from the future: Collaborative robots
Collaborative robots are a type of industrial robot. They were initially designed to meet the customized and flexible manufacturing requirements of small- and medium-sized enterprises, and perfectly align with the development trends of the manufacturing industry. Collaborative robots are suitable for jobs that people are unwilling to do, such as highly repetitive work like sorting and packaging. Collaborative robots have several unique advantages:
Safer: Collaborative robots are compact and intelligent, and their sophisticated sensors enable them to stop in an instant.
Faster and more flexible deployment: Collaborative robots feature user-friendly programming, such as programming by demonstration, natural language processing, and visual guidance. They can be placed in new positions at any time, and programing and commissioning can be completed rapidly, so they can start working very quickly.
Lower total cost of ownership (TCO) and shorter payback period: The price and annual maintenance cost of collaborative robots are significantly lower than those of traditional industrial robots.
Snapshot from the future: Autonomous mobile robots
Autonomous mobile robots (AMRs) are a key enabler to help the manufacturing industry become flexible and intelligent. They will reshape the production, warehousing, and logistics processes.
- On production lines, AMRs make automated and unmanned logistics possible. This includes unmanned execution.
- In warehouses, AMRs implement goods-to-person picking, executing intelligent picking, movement, and stock-in and stock-out procedures.
- AMR systems can be expanded to an entire campus. For example, when goods are unloaded, robots can automatically move them into their designated warehouse. Goods will be automatically logged into and out of warehouses, and the movement of goods between factories or warehouses will be automatically registered.

New production models geared towards personalized needs
Snapshot from the future: ICT-powered flexible manufacturing
Flexible manufacturing is an advanced production model characterized by on-demand production. It helps companies become more flexible and enables them to rapidly respond to ever-changing market demand. In addition, flexible manufacturing shortens the R&D cycle, cuts R&D costs, and ensures equipment is not left idle, while reducing inventory risks and speeding up capital turnover.
- Flexibility of product design and production line planning: After receiving an order for a new category of product, companies need to quickly conduct R&D and design, and rapidly adjust factors such as production line equipment, working procedures, processes, and batch size. This is where ICT comes in. Simulation, modeling, VR, and other ICT technologies can be used to simulate the entire new manufacturing process. This will reduce the cost of new product development and design, and support more accurate adjustment cost projections and capacity projections.
- Flexibility of process: In flexible manufacturing, companies can design products based on the personalized needs of customers, or invite customers to directly participate in product design (e.g., using modular systems to enable customers to define what a product will ultimately look like). Both models require The intelligent scheduling system. The system makes automatic adjustments and provides an optimal production plan based on known features such as the factory's production capacity, order complexity, and delivery deadlines.
- Flexibility of equipment: In the future, ICT technologies such as visual programming, natural language interaction, and action capture will help factories reprogram equipment quickly and easily. This will help companies promptly meet consumer demand for flexible manufacturing.
- Flexibility of logistics: One of the keys to flexible manufacturing is modularization, through which a large number of finished components are manufactured. This requires automated ICT technology to effectively manage warehousing and logistics, which prevents omissions and other errors in the shipment process.

Resilient and intelligent supply chains that help enterprises respond to crises
Snapshot from the future: Supply chain visualization powered by digital technologies
Supply chain visualization is about using ICT technology to collect, transmit, store, and analyze upstream and downstream orders, logistics, inventories, and other related information on the supply chain, and graphically display the information. Such visualization can effectively improve the transparency and controllability of the whole supply chain and thus greatly reduce supply chain risks.
- Supply chain visualization supports the tracking of materials and equipment in upstream activities. Logistics information is displayed in real time and goods can even be traced throughout the production process.
- With supply chain visualization, the operation data of various transportation vehicles in the logistics system is also available, and the status of these vehicles can be displayed in real time.
- A remote monitoring system monitors the environment in warehouses in real time. This system uses various sensors to graphically display operations and maintenance (O&M) information such as temperature, humidity, dust, and smoke.
Snapshot from the future: From supply chain to supply network
With the adoption of ICT technologies such as cloud computing, IoT, big data, and AI, the supply chain will transform into a supply network. In this network, the upstream materials required by every link have multiple alternative sources, and they can be sourced through multiple routes. A multi-contact collaborative supply ecosystem will be created by enhancing the internal and external interconnectivity of enterprises. The failure of any single link will not result in paralysis across the whole supply network.
More Outlooks
